Excavations in the rocky surface are an integral component of geological inspection. Boreholes are bored to acquire specimens of soil and stone from the ground’s bowels and to document the properties of the rock layers. In addition, boreholes may also be deployed to insert monitoring contraptions, like seismographs, for gauging seismic activity in the locale.
To form drill holes, a rotary or percussion drill bit is employed, depending on the size and composition of the strata. Typically, larger chasms call for the application of a rotary drill bit, while more miniature cavities utilize percussion bits. Subsequently, the pickaxe is linked to a drill line and dropped into the cleft before being precisely circulated to make the hollow.
When drilling a hole, it is essential to consider its depth. As the depth increases, so does the cost of the job; what’s more, maintaining stability of the drill string grows progressively tougher. To avert getting stuck in the hole, the drill string needs to be regularly removed from it.
When it comes to drilling a hole, the type of rock is a factor not to be overlooked. The type of rock, e.g. granite, shale, or limestone, dictates the type of drill bit and the amount of torque needed to make progress. Moreover, each type of rock has its own level of friction which, naturally, influences the rate and efficiency of the drilling procedure.
The magnitude of the second stage is a pivotal point when perforating something. As a general rule, the more impressive the specifications, the more expensive the drilling will be. Additionally, by increasing the dimensions, the entire drill string becomes more prone to inconstancy.
To ensure a successful drilling process, careful consideration should be given to the type of drill hole casing to be used. This casing is essential for sustaining the hole and protecting the rock from further destruction. Typically, steel casing is suitable for holes of larger diameters, while plastic casing is ideal for more modest-sized holes.
Knowing which type of drill bit to use when drilling into rocky terrain is paramount to ensuring the speed and efficacy of the process. Typically, carbide bits are employed in harder rock types while diamond bits come in handy for softer rocks. Drill bits also vary in their torque levels, thereby influencing the performance of the drilling process.
All in all, drilling into bedrock is an indispensable component of geological assessment. Before engaging in the drilling process, several elements must be evaluated comprehensively and strategically, including both the depth and magnitude of the hole, as well as the type of rock being operated on and the drill bit being used. Additionally, considerations should be made for the casing type chosen to ensure a reliable and risk-free procedure. By carefully examining all these details prior to initiating the drill, it is possible to complete operations with maximum effectiveness and security.
Boring through rock is a universally accepted means of retrieval from underneath the surface. Rigging up tunnels, or removing ore, as well as various geological forms can all be made possible through drilling holes. Samples present in the substratum can also be accessed for scientific inquiries, owing to such an apparatus.
The art of drilling into rock is quite the feat. Starting with a drill bit affixed to the end of the rig, it is methodically lowered to the predetermined spot and set into motion. Spinning at an accelerated rate, the bit plunges into the rock and produces the desired hole.
To bore a hole, a drill bit made of tough material such as steel or diamond must be employed. The type of bit used depends on the hardness of the rock; softer rocks can be managed with steel, whereas diamond is better suited for harder types. With the drill bit attached, the rig is simply moved in an up and down motion to dig a hole.
Holes drilled into hard rock are crucial for a variety of fields. In mining, drill holes are employed to make passages, acquire ore, and build other geological components. Additionally, scientists utilize these same openings to extract material from deep in the ground for additional research.
With an eye towards energy resources, oil and gas companies deploy drill bits to bore down into reservoirs. With the drill bit rotating at a swift velocity, the steel or diamond material can burrow through the hard bedrock and form a channel. Then, as the rig is slowly shifted back and forth, this bit is constantly raised and lowered to expand on the central bore. In this way, these firms can acquire access to coveted oil and gas reserves.
Drilling holes is a staple in the construction industry, especially for the incorporation of pipes and wires into concrete walls. But this tactic isn’t limited to such durable materials. Holes in rocks and boulders are now routinely made when constructing roads and bridges, demonstrating the flexibility of this tool.
Drilling into solid rock can be a risky task, so it is essential to wear safety gear and strictly abide by safety measures. If the drill bit isn’t maintained with care, it can easily become stuck or even break, thus exposing everyone to possible danger and harm.
Creating pathways into rock is a crucial facet of many industries and businesses. Whether it’s accessing reservoirs of oil and gas, establishing tunnels to mine ore, or gathering samples from the depths of the earth for research purposes, drilling holes is essential. Moreover, in the development sector, drills are necessary for running conduits and wires as well as constructing roads and bridges. Taking the necessary precautions with the right safety equipment and following all safety protocols is paramount for all involved in drilling operations.
Related Product
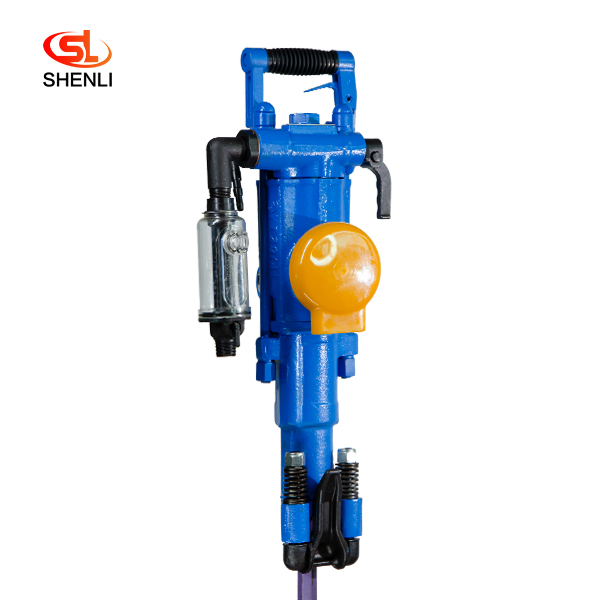
YT29A Air Leg Pneumatic Rock Drill Pusher Leg Rock Drill
YT29A air-legged rock drills are heavy-duty push-leg (air-legged) rock drills with low energy consumption, which are more suitable for drilling horizontal or inclined holes in medi […]
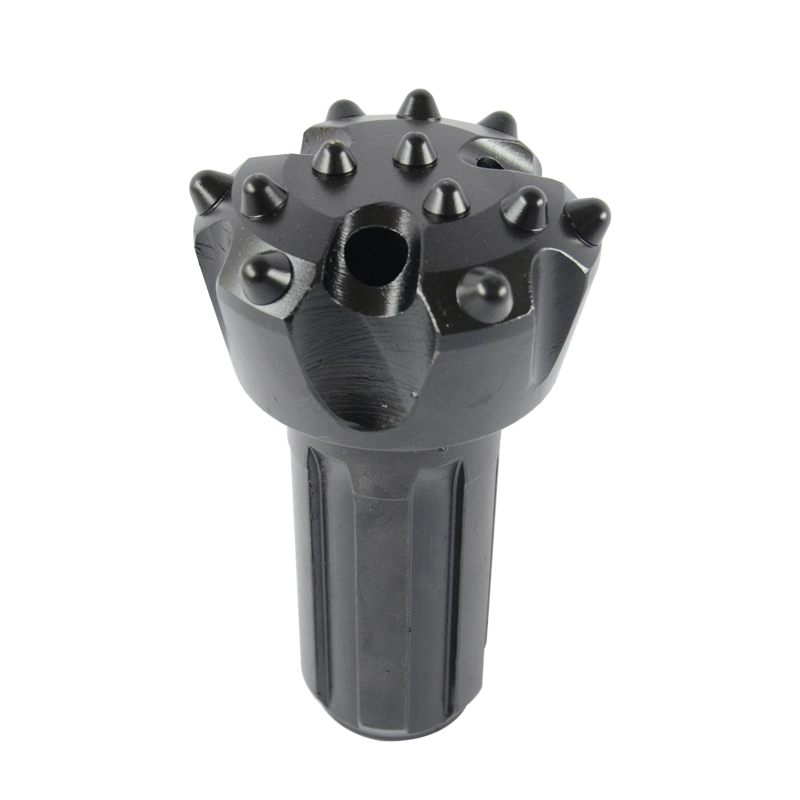
Cir Series Dth Bits(Low Pressure) Cir90-90
Down-the-hole (DTH) hammer bits are used with Down-the-hole hammers for drilling holes through a wide range of rock types. In conjunction with DTH hammers, drill hammer bits are de […]
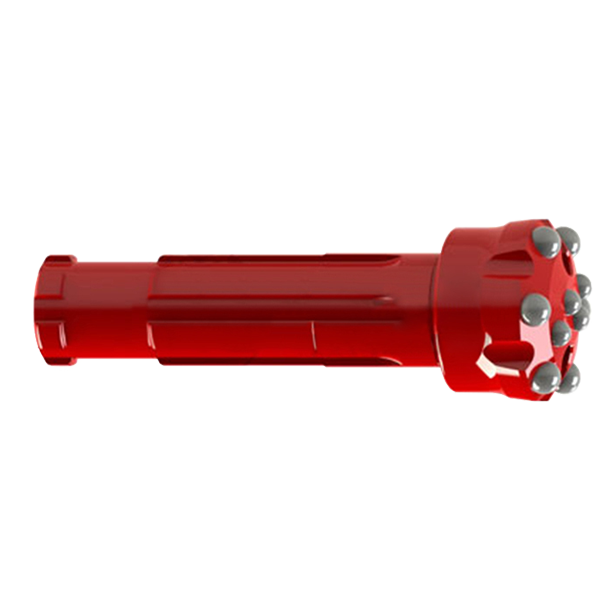
DHD Series DTH Bits(High Pressure) DHD
high pressure drill bit is mainly used in geological exploration, coal mine, water conservancy and hydropower, highway, railway, bridge, construction and construction, etc. Advanta […]
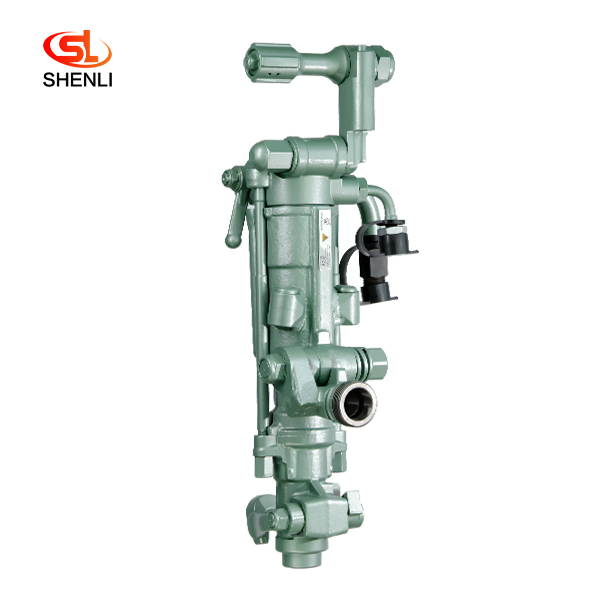
S250 Air Leg Pneumatic Rock Drill Pusher Leg Rock Drill
(S250 jackleg Drill) has been the preferred choice of miners who demand high performance, superior control and lasting reliability. the S250 jackleg allows operators to drill in co […]
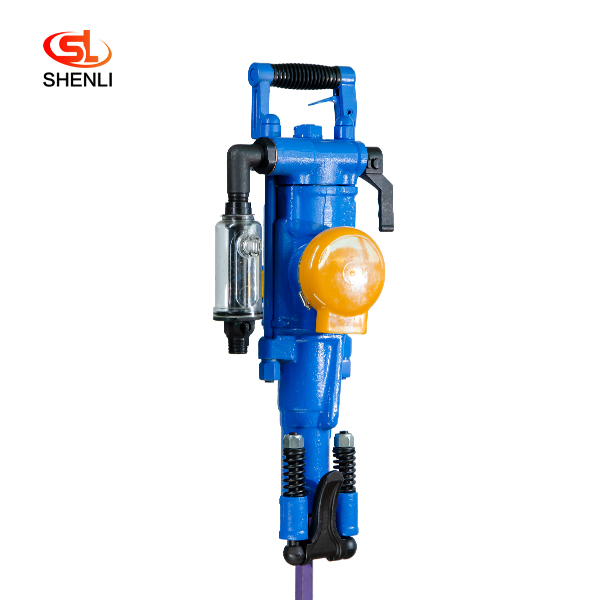
YT28 Air Leg Pneumatic Rock Drill Pusher Leg Rock Drill
The YT28 air-leg rock drill is a kind of high-efficiency, energy-saving and environmentally friendly rock drilling equipment. Compared with similar pneumatic products, the YT28 air […]
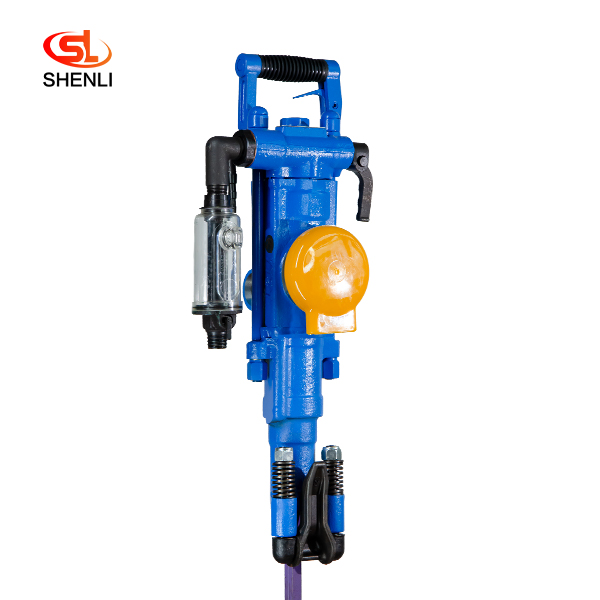
YT27 Air Leg Pneumatic Rock Drill Pusher Leg Rock Drill
The YT27 air-legged rock drill is a highly efficient lightweight rock drill suitable for downward or inclined drilling in medium-hard or hard (f=8 – 18) rock with a diameter […]
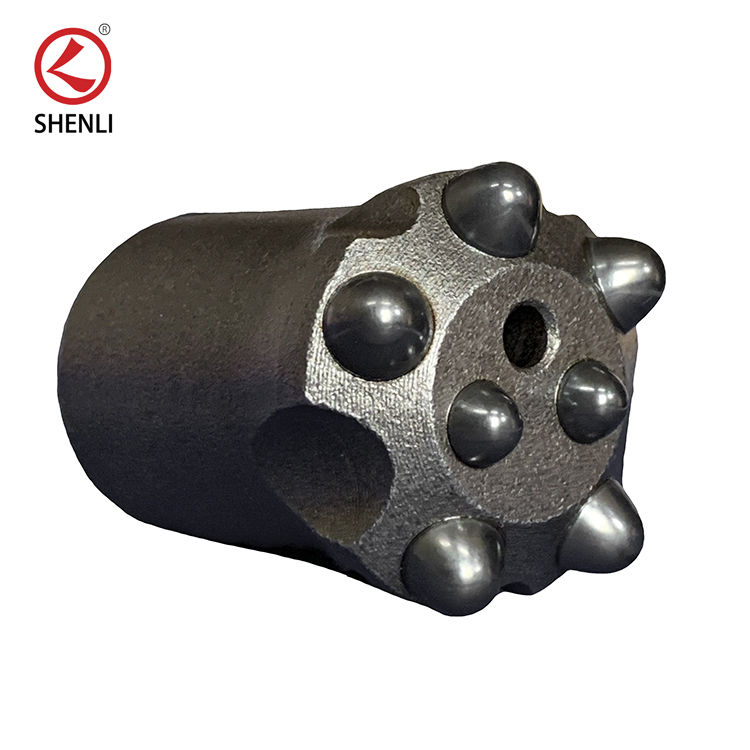
Taper Bits
Taper bits, especially Tapered button bits are the most popular tapered drill bits with a wide selection of head diameters from 26mm to 48mm. With carbide buttons cold pressed on t […]
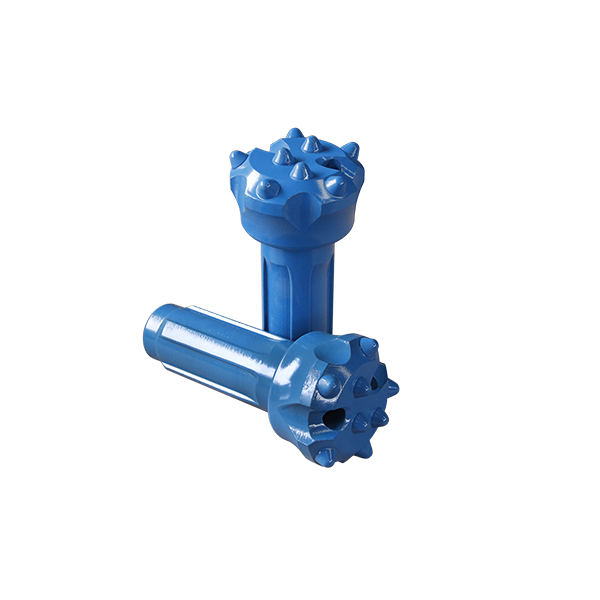
CIR Series DTH Bits(Low Pressure) CIR76-76
Down-the-hole (DTH) hammer bits are used with Down-the-hole hammers for drilling holes through a wide range of rock types. In conjunction with DTH hammers, drill hammer bits are de […]
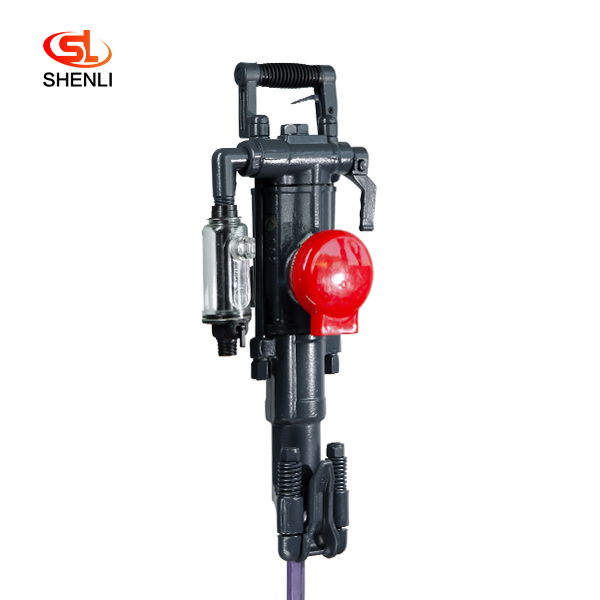
S82 Air Leg Pneumatic Rock Drill Pusher Leg Rock Dril
Model S82 air-legged rock drills are heavy-duty air-legged rock drills with high efficiency and low consumption, which are especially suitable for use in the construction of railro […]
Post time: 2023-07-14