A rock drill is an engineered device specifically created for creating apertures in rock. This tool may be driven by either an air compressor or an electric motor, making it applicable in industries varying from exploration, quarrying, and construction.
In the early 1800s, England witnessed a revolution of sorts with Daniel Turner, a blacksmith, dreaming up the first rock drill. This hand-operated invention changed the ballgame for coal miners, providing an uncomplicated method to bore holes for extracting precious fuel.
In the year 1848, Joseph W. Fyfe—an Englishman—conceived the first pneumatic rock-drilling device. By utilizing compressed air, it operated more effectively than Turner’s earlier construction.
By the 1800s, the construction industry had begun to embrace the use of rock drills. These helpful tools enabled builders to create holes for structures such as foundations, piers, and tunnels with greater ease.
Rock drills have diversified uses in multiple industries, such as mining, quarrying, and construction, but also in oil and gas as well as geothermal drilling. Today, these robust tools are utilized to support various applications.
With multiple shapes and sizes, rock drills are commonplace tools, particularly the rotary drill which uses a spinning drill bit to get the desired results.
The second type of drill employed for cutting through rock is the percussion drill. It operates by striking at the work surface, using a pounding motion to penetrate and create holes.
When it comes to drilling through hard rocks like granite, the diamond drill is the go-to tool. As one of three types of rock drills, this specialized equipment proves effective against even the toughest materials.
Whereas most rock drills are powered through the force of compressed air, an alternative option involves running them on electric motors.
To power a rock drill, compressed air is requisite – and thus air compressors are a staple of the process, providing the power which allows the tool to operate.
For drilling rocks, there are two common types of drills: ones that run on electricity and those driven by air pressure. Generally, electric-powered drills are more lightweight and can be moved around easier than their air-powered counterparts.
The drill bit at the tip of a rock drill is manipulated by a handle attached to it through a drill steel. This steel device functions as a bridge, allowing the operational force of the handle to be transferred to the bit beneath.
Cutting into rock requires more than just a drill–the drill bit is the indispensable tool that makes a hole. Different drill bits are designed for particular sizes and types of drilling, allowing for precision in every job.
The size of the desired hole will decide the accompanying drill bit required while the type of rock to be pierced will dictate its appropriate shape.
Constructed from an array of substances, drill bits, according to their intended function, can be composed of steel, diamond, carbide, or tungsten carbide. The most popular option is steel.
Although diamond drill bits are pricey, they outperform all other drills when it comes to drilling hard materials. Carbide drill bits are cheaper than diamond varieties, yet they lack the same level of effectiveness when dealing with tough surfaces.
Although tungsten carbide drill bits are budget-friendly, unfortunately the tough outer layer of hard rocks is simply too much for them to handle.
As a critical element, the RPM or revolutions per minute of the drill must be taken into account. This numerical indicator illustrates how fast the drill is able to rotate.
A sharp rate of rotation leads to expedited drilling, but also increases deterioration from usage.
The longevity of a drill bit is influenced by the particular material used and its rate of application. For example, steel-constructed bits tend to outlast their carbide counterparts.
Durability is a major advantage when it comes to carbide drill bits, as they will provide hardworking longevity compared to tungsten carbide drill bits.
The longevity of the drill bit is heavily dependent on the type of rock it is being applied to; sandstone and shale, for example, will quickly diminish its effectiveness, compared to drilling through granite and other harder rocks.
Hard rocks can cause the drill bit to overheat, consequently leading to its breakage.
When penetrating into difficult rocks, it is indispensable to utilize a drill bit assembled from a material that can tolerate the sultry temperature.
When it comes to this application, diamond and tungsten carbide really can’t be beat.
When it comes to preserving the life of a drill bit, one factor to consider is the size of the hole being made. If the hole is on the smaller side, it will be more likely to reduce the lifespan of the bit in comparison to creating a larger hole.
A deeper hole will increase the amount of heat produced by the drill bit, thus shortening its life span. Heat is an inevitable force as the deeper the well, the more energy and friction created, exhausting the drill bit quicker.
The longevity of any drill bit diminishes as the depth of the hole augments.
To prolong its lifespan, a drill bit requires an adequate cooling regimen, fulfilled by a special fluid known as a coolant. Through its regulation of the bit’s temperature, the coolant ensures its sustained efficiency against damage from overheating.
Cooling is an often-times tricky process, yet water and oil are both possible solutions to the problem. The former is more popularly employed, but the latter can still prove an efficient means of keeping things cool.
Chilling Agent for Quality Performance
Related Product
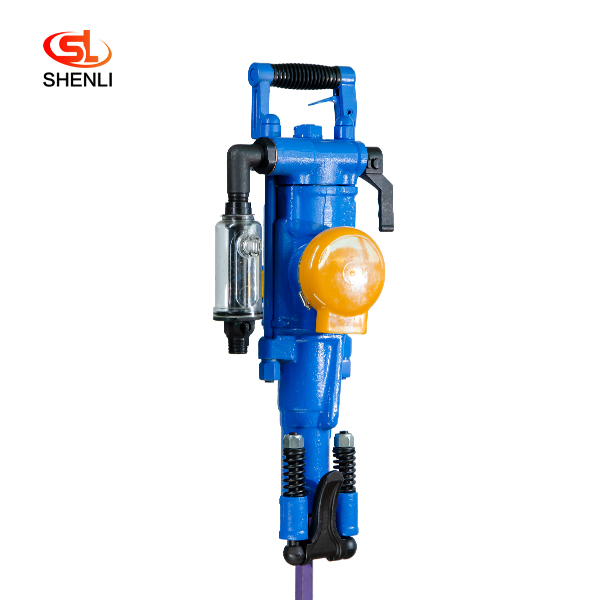
YT28 Air Leg Pneumatic Rock Drill Pusher Leg Rock Drill
The YT28 air-leg rock drill is a kind of high-efficiency, energy-saving and environmentally friendly rock drilling equipment. Compared with similar pneumatic products, the YT28 air […]
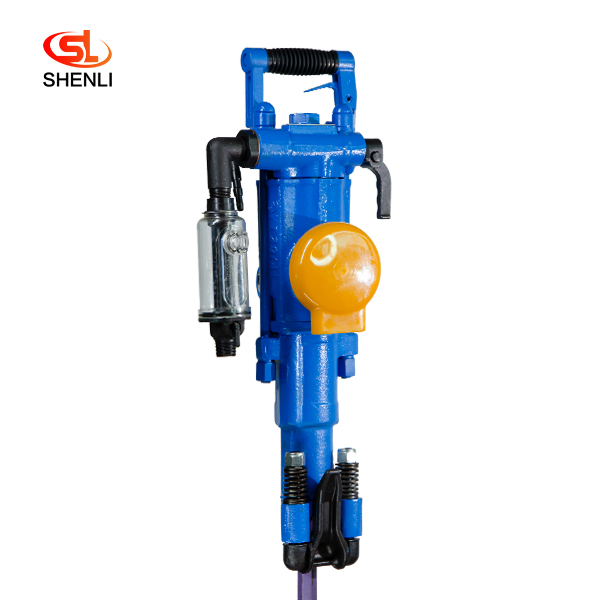
YT29A Air Leg Pneumatic Rock Drill Pusher Leg Rock Drill
YT29A air-legged rock drills are heavy-duty push-leg (air-legged) rock drills with low energy consumption, which are more suitable for drilling horizontal or inclined holes in medi […]
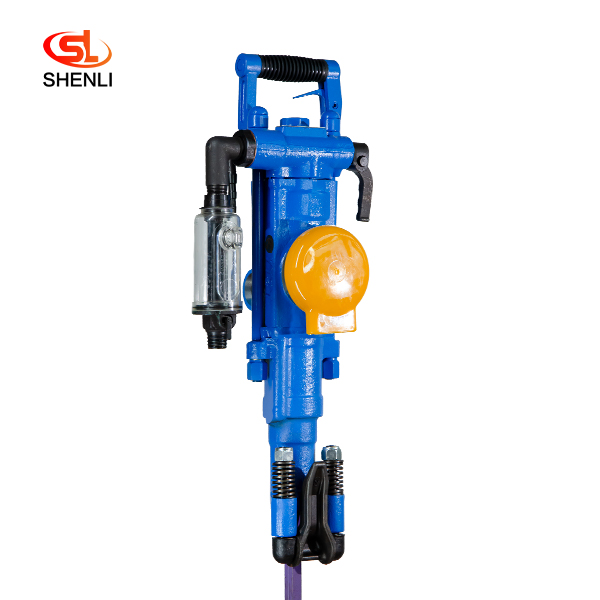
YT27 Air Leg Pneumatic Rock Drill Pusher Leg Rock Drill
The YT27 air-legged rock drill is a highly efficient lightweight rock drill suitable for downward or inclined drilling in medium-hard or hard (f=8 – 18) rock with a diameter […]
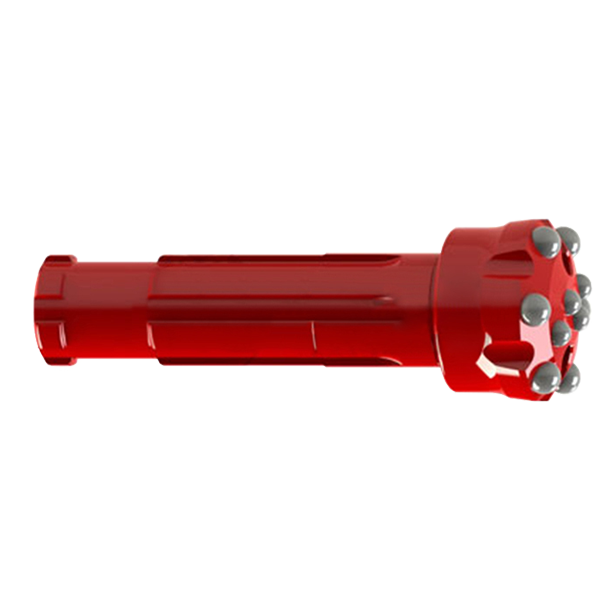
DHD Series DTH Bits(High Pressure) DHD
high pressure drill bit is mainly used in geological exploration, coal mine, water conservancy and hydropower, highway, railway, bridge, construction and construction, etc. Advanta […]
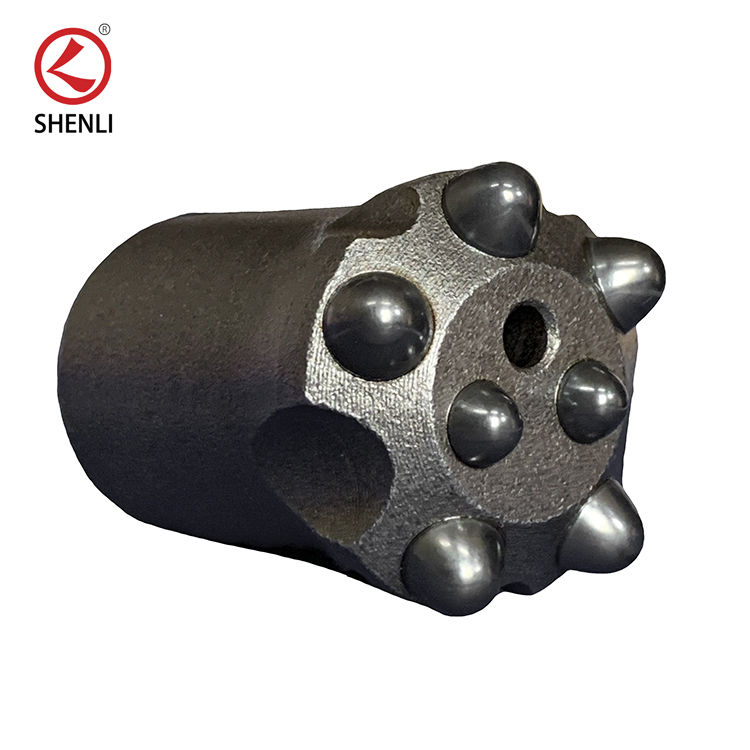
Taper Bits
Taper bits, especially Tapered button bits are the most popular tapered drill bits with a wide selection of head diameters from 26mm to 48mm. With carbide buttons cold pressed on t […]
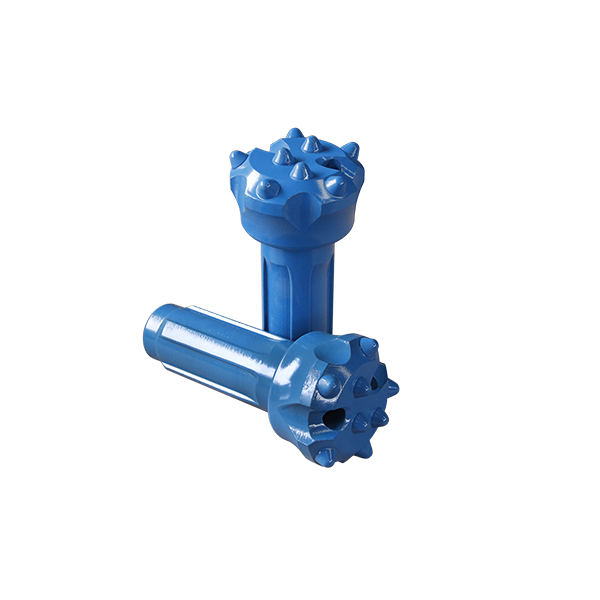
CIR Series DTH Bits(Low Pressure) CIR76-76
Down-the-hole (DTH) hammer bits are used with Down-the-hole hammers for drilling holes through a wide range of rock types. In conjunction with DTH hammers, drill hammer bits are de […]
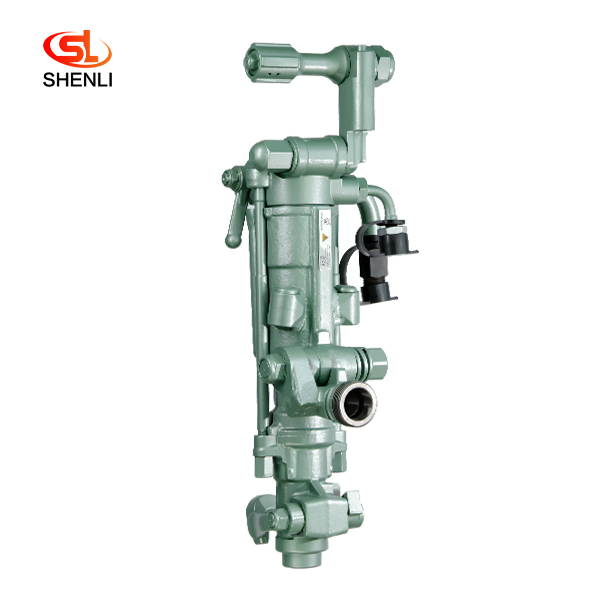
S250 Air Leg Pneumatic Rock Drill Pusher Leg Rock Drill
(S250 jackleg Drill) has been the preferred choice of miners who demand high performance, superior control and lasting reliability. the S250 jackleg allows operators to drill in co […]
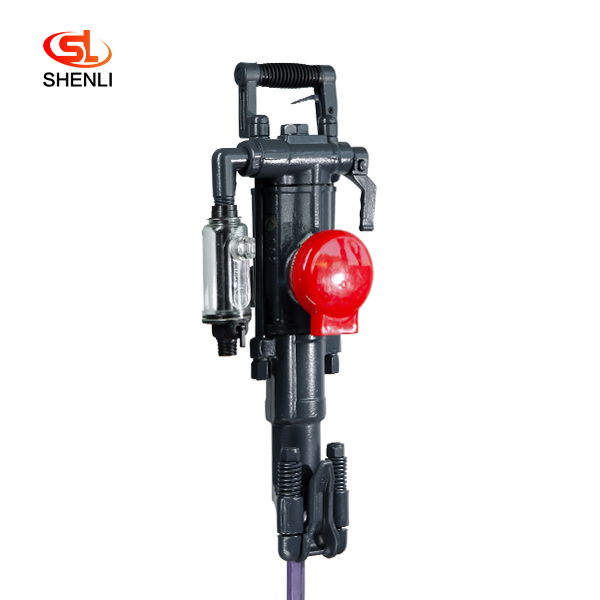
S82 Air Leg Pneumatic Rock Drill Pusher Leg Rock Dril
Model S82 air-legged rock drills are heavy-duty air-legged rock drills with high efficiency and low consumption, which are especially suitable for use in the construction of railro […]
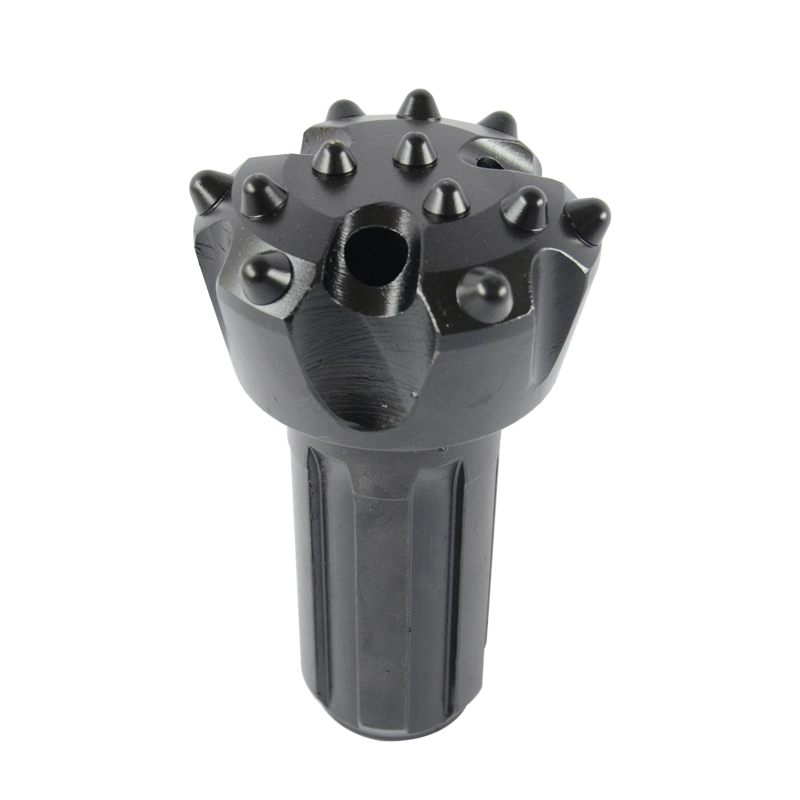
Cir Series Dth Bits(Low Pressure) Cir90-90
Down-the-hole (DTH) hammer bits are used with Down-the-hole hammers for drilling holes through a wide range of rock types. In conjunction with DTH hammers, drill hammer bits are de […]
Post time: 2023-06-22